Innovative construction solutions designed to optimize costs and reduce build time, delivering immediate savings and efficiency
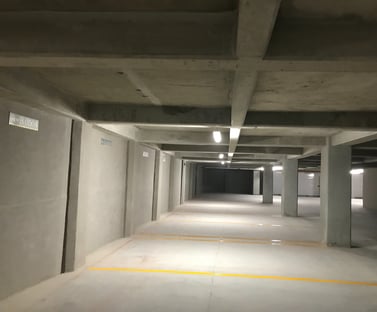
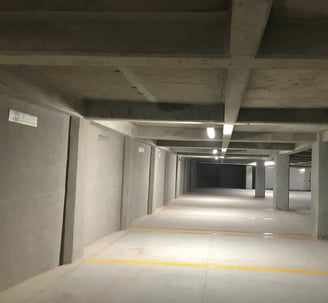
System of retaining walls for underground parking lots and protection of adjoining buildings
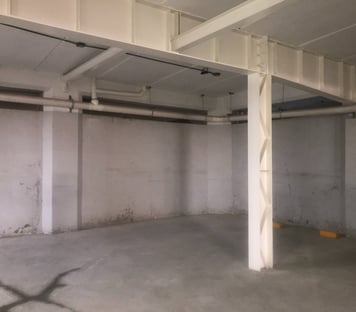
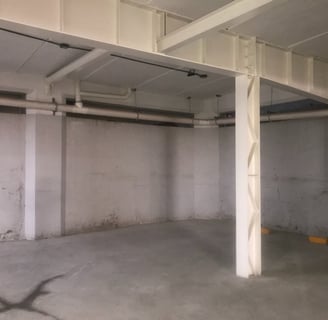
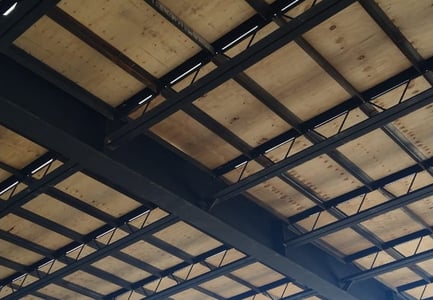
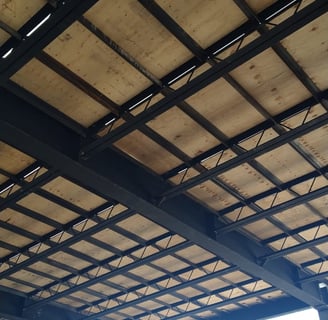
PRODUCTS AND SYSTEMS
PRODUCTS THAT WE ARE OFFERING
We are basically offering FOUR products that provide immediate benefits for your project, high safety system, through a lower cost and faster construction process:
1.- (A-B) SFS® system of retaining walls in underground parking lots and protection of adjoining areas. No need for anchors or temporary walls or disposable bracing system.
2.- (D) JOISTS SFS®-type suspended slabs system, which is very quick to build and weighs much less than any other system of slabs, either for parking lots or for superstructures.
3.- (A-C) Building system identified as "UP-DOWN", which allows erecting the superstructure before starting the excavations for underground garages.
4.- SFS® system for sound barriers in residential areas attached to highways or airports.
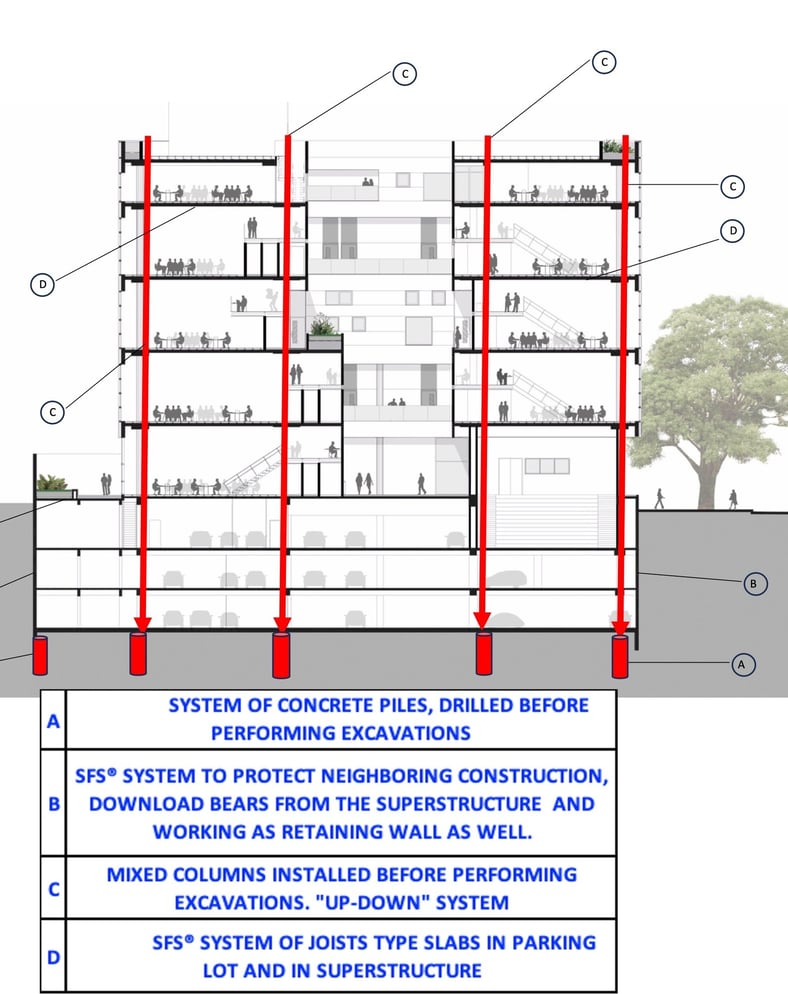
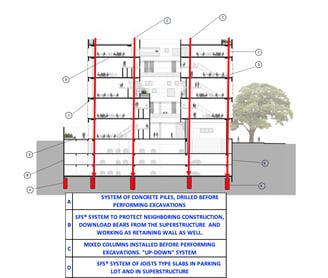
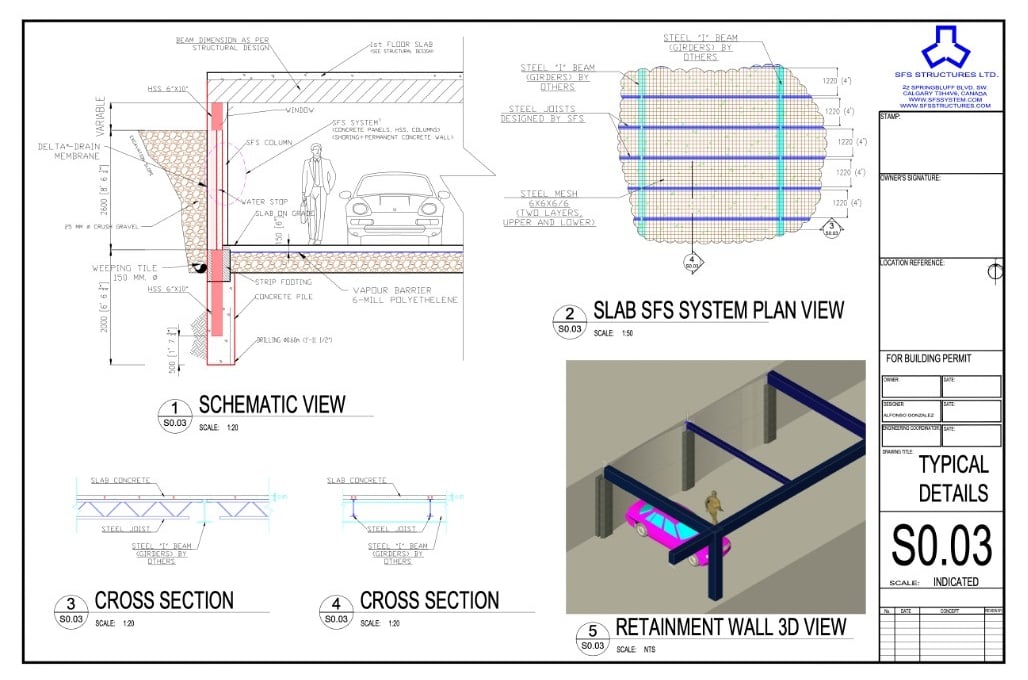
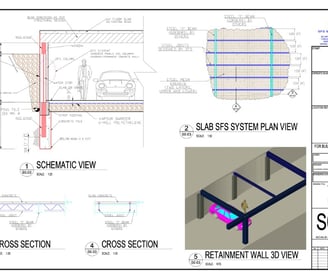
We want to help make your new project a reality with greater security, at a lower cost and faster in the construction process.


About Us
We are a design and construction company established in ALBERTA, CANADA, which offers service to the whole world, made up of professionals with experience in residential, commercial, industrial, hospital construction and in general retaining walls, suspended slabs and protection systems for slopes stabilization and neighbour's constructions.
We offer technical advisory, supervision and control of work in general.
We provide FREE quotes, starting at the initial stage of the project BEFORE construction begins.
Contact Us
For further information, please fill out the next form with your data and we will contact you ASAP. If you wish, you can send us an email to :
civil@sfssystem.com
or via WhatsApp to the next number :
+1-403-615-9341